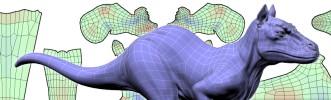 |
headus 3D tools / 3D scans Support Forums
|
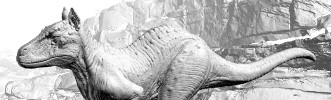 |
View previous topic :: View next topic |
Author |
Message |
meeotch
Posts: 1
Joined: 14 May 2011
|
Posted: Sat May 14, 2011 9:11 am Post subject: uvlayout for manufacturing |
|
|
I'm evaluating UVLayout for an art school here in NYC. First off: awesome tool!
Our application is peeling and flattening arbitrary surfaces for manufacture out of paper, plastic, sheet metal, etc. I'm noticing that just by re-flattening individual islands, you can get some pretty different resulting shapes. I'm assuming some of these are more "right" for manufacture than others.
So the first question would be: in terms of the amount of "distortion" shown, what does that mean, exactly - size/angles of individual polys? Some measure of local angles between polys? I'm trying to determine whether it's acceptable to just try to get everything to be light green, and trust that the resulting shape actually makes sense in the physical world.
Second question: presumably, one important criterion for manufacture would be to keep the lengths of seams equal on both sides. (So, for instance, if you cut an arm off a model, or remove an eye socket in order to get undistorted flattened pieces.) Is there any way to accomplish this, while allowing UVLayout to determine the optimal shape of the seams?
Final question: any way of determining areas of multiple curvature? When working with, say, sheet metal you'd presumably want to limit the curvature to one direction at each point in order to end up with developable surfaces. |
|
Back to top |
|
 |
headus Site Admin

Posts: 2902
Joined: 24 Mar 2005
Location: Perth, Australia
|
Posted: Sun May 15, 2011 6:50 pm Post subject: Re: uvlayout for manufacturing |
|
|
"by re-flattening individual islands, you can get some pretty different resulting shapes. "
I would have said slightly different maybe. If they're very different, then it could be that the shells are getting twisted and need some user encouragement to sort things out. Hard to say without pics.
"in terms of the amount of "distortion" shown, what does that mean, exactly - "
Purely area. Angles are usually quite good after flattening; when you apply the checker texture in the "3D" view, it should look nice and square. Its the area of the polys that will vary.
"whether it's acceptable to just try to get everything to be light green, and trust that the resulting shape actually makes sense in the physical world."
That's my feeling for it. UVLayout wasn't ever intended to be used as a pattern maker, but if you can get things as close to green as is practical, then the shapes should be very close to ideal.
"one important criterion for manufacture would be to keep the lengths of seams equal on both sides."
Agreed, but unfortunately that's something that UVLayout doesn't currently do. If you aim for as much green as possible though, the seams will naturally tend towards being the same lengths.
"any way of determining areas of multiple curvature? "
Not currently, but if its not green, then that would be a sign of curvature in two directions.
How complex are your shapes? If the material you are working with has no give to it (i.e. sheet metal) you may want to build up your patterns from the individual polys, instead of trying to flatten shells.
Have a look at the "Segment" tool, and in particular the fast weld mode. The idea is that the mesh is broken down into many pieces, these are flattened, and then you weld it all back together to create the pattern. By flattening smaller pieces, you're pretty much guaranteed that all polys are perfectly flat, and in turn all your seams will be the perfect length.
Phil |
|
Back to top |
|
 |
|
|
You cannot post new topics in this forum You cannot reply to topics in this forum You cannot edit your posts in this forum You cannot delete your posts in this forum You cannot vote in polls in this forum You cannot attach files in this forum You cannot download files in this forum
|
Powered by phpBB © 2001, 2005 phpBB Group
|